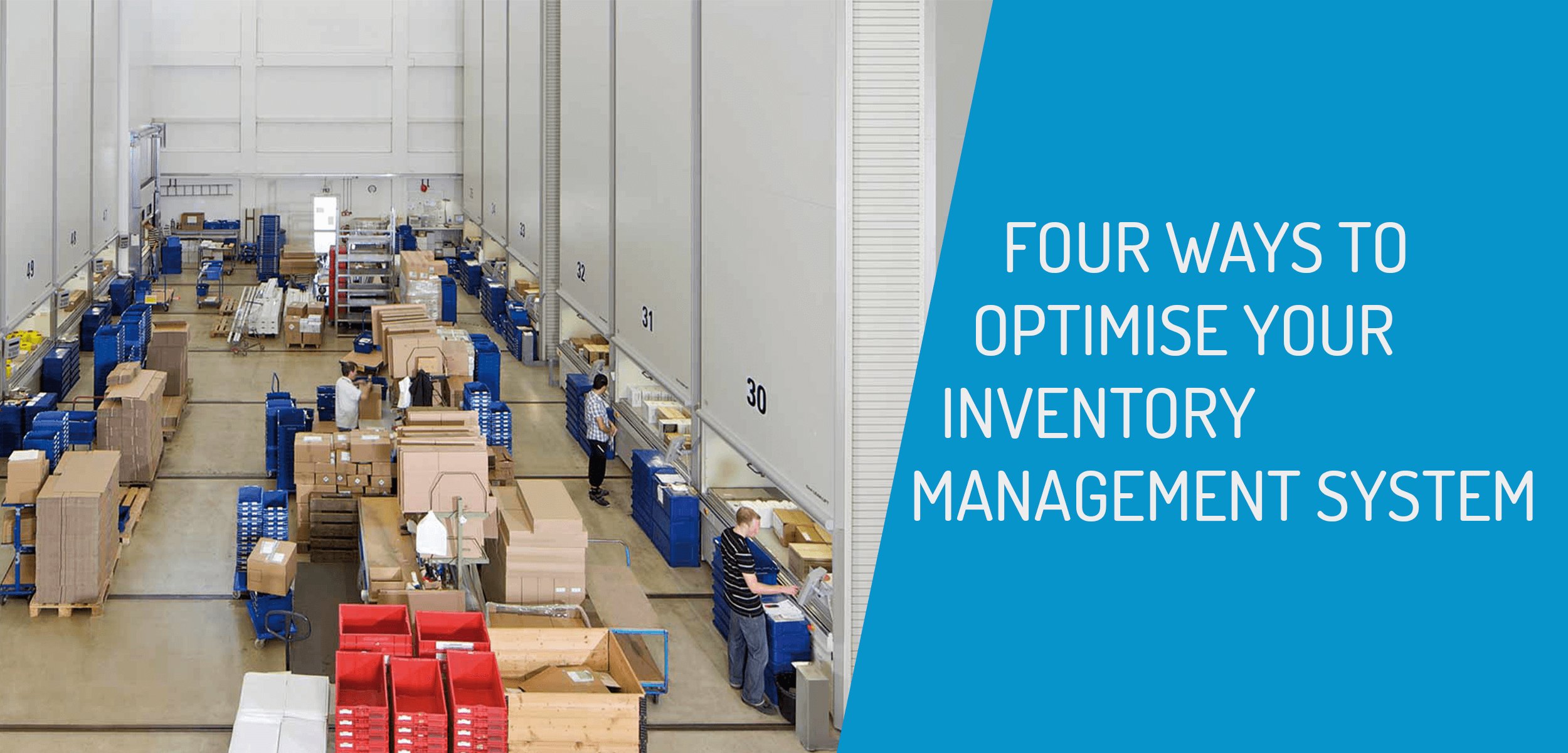
How You Can Optimise Your Business, With Inventory Management Software
Save time, money and double handling with MultiPick inventory management software. This is your order batching and put-to-light management system. A globally trusted solution, it improves your picking and putting speed, order accuracy and inventory control. MultiPick is cost-effective, with extra service support throughout your software’s life cycle. MultiPick is a hardware and firmware control system. With firmware, there are no operating system or software maintenance overheads. Designed for your Hänel storage systems, it enhances functionality and performance.
Here are four ways MultiPick can help you and your business.
1. Quick and easy “plug-and-play” integration.
MultiPick uses advanced algorithms and a self-learning capability. This makes the lift operator highly efficient and productive. You can learn the system in only a few minutes. Follow simple instructions during the pick-put process. Eliminate errors simply by pressing a confirmation button for most operations. MultiPick connects to the local network and your Haenel Lean Lift or Rotomat. It will divert sent Jobs to the Hänel lifts into a Batch picking process. It manages the data transfer between your ERP/WMS software, the Hänel lifts and the Put Bench.
2. High pick rates and order volume.
MultiPick inventory software management increases operator productivity and efficiency. It reduces total picking times and completion of all Jobs. An automated Batch picking solution requires a “Put Bench.” This is where many Jobs/Orders are simultaneously processed. This bench is equipped with a series of displays (i.e. put-to-light indicators). Each display represents one Job/Order. They guide Hänel lift operators where and in what quantity, to place picked items. They synchronise with lift picking operations via sophisticated hardware and software control systems. With Batch picking, Hänel lifts only need a single shelf retrieval to pick at once. It picks all the required quantity for every Job at the Put Bench.
3. Batch pick and batch manage your jobs.
When picking an item, you can organise enough quantity to fulfil several Jobs or Orders in one pick. This reduces picking time. For example: If 3 Jobs each need two of the same item, in serial picking 2 items are picked at 3 separate times. With batch picking, only one pick is done. Six items are picked, and two are immediately placed into each of the three orders. This means your picker is only picking that inventory item once. Batch picking requires a sophisticated electronic system to keep track of picked items. It ensures the correct quantity is placed into each Job or Order. Your operator can retrieve the same shelf and pick the same item, as many times as required.
4. Sequential or serial picking with Multipick batch picking solution.
Hänel lifts will instruct the lift operators to pick items for one Job at a time. Once that Job completes, the next Job commences. This improves productivity. By bringing the inventory to your picker (goods-to-person principle), they don’t need to search for it themselves. This is very effective in lower pick volume environments. It eliminates wasted time looking for the required items that need picking.
For more manufacturing and machinery tips and news, subscribe today.
Headland Australia can help you with efficient storage strategies for your warehouse. This includes specialist warehouse storage solutions and management environments. With advanced Hänel microprocessor controller units, we provide complete warehouse management systems. These include high-speed batch picking, tool management processing, etc.